ソリューション
製品設計
近年、ものづくり分野では国際的な競争が激化しており、自動車業界をはじめとする多くの分野で、開発期間の短縮が求められています。その一方で、設計現場では若手技術者の担い手が不足しており、知識や経験の継承体制を十分に構築できていないことが課題となっています。本ページでは、こうした製品設計の現場における課題に対し、Multi-Sigma®を活用したアプローチをご紹介します。
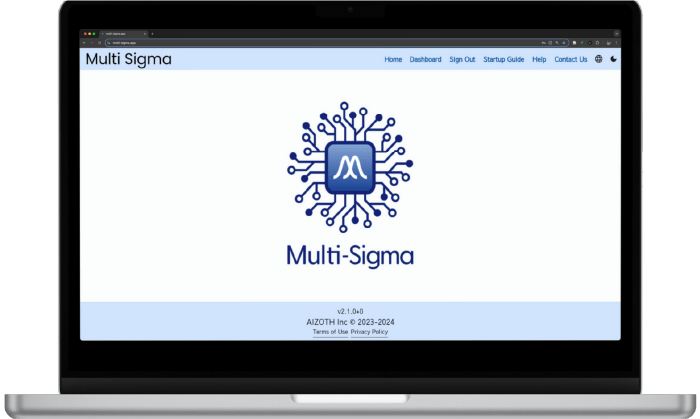
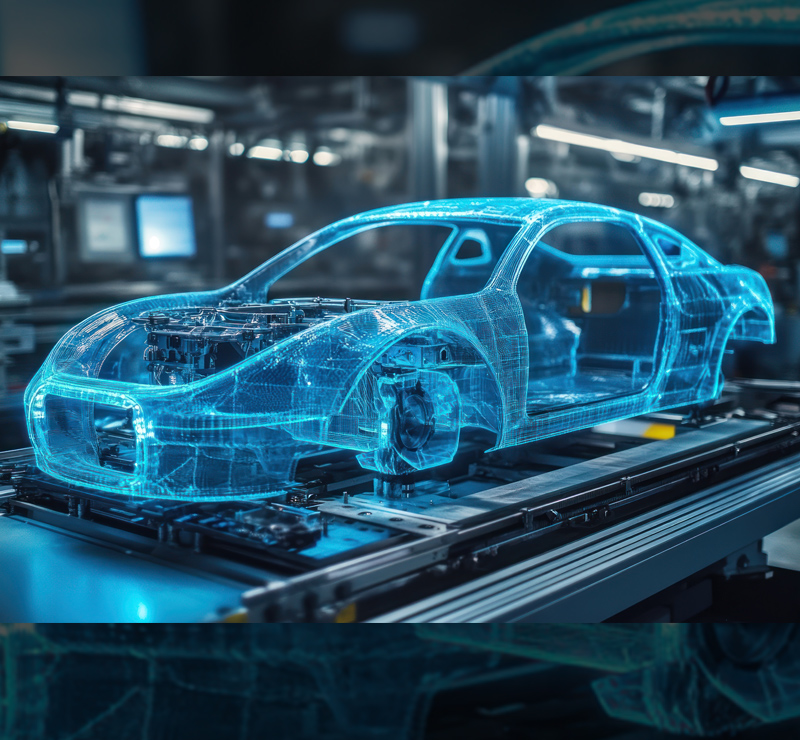
製品設計における課題
複雑化する製品と要求仕様
近年の製品設計では、航空機や自動車に代表されるように、高度なコンピュータやソフトウェアを組み込んだシステム全体の設計が求められています。ハードウェアとソフトウェアの高度な連携により、性能・品質・安全性等の要件を高水準で満たす必要があります。さらに、安全法規や機能安全(Functional Safety)などの要件対応も不可欠です。こうした背景のもと、システムズエンジニアリングに基づくモデルベース開発(Model-Based Development: MBD)が注目されていますが、制御対象のモデリングやシミュレーションの構築には多大な工数が必要で、効率化が求められています。
開発期間の短縮と技術的要件の高度化
近年、カーボンニュートラルやソフトウェア定義型製品(Software-Defined Product)への移行といった社会的・技術的変化を背景に、自動車業界では新興プレイヤーの参入や製品構造の変革が進み、開発競争がかつてないほど激化しています。こうした傾向は、自動車業界に限らず、エレクトロニクスや産業機器など他の製造分野においても、グローバル競争や市場変化への迅速な対応が求められる中で、開発期間の短縮が強く求められる共通課題となっています。その一方で、製品が満たすべき技術的要件は年々高度化しており、安全性・性能・EMC(電磁両立性)などの多様な検証を伴うことが一般的です。構造解析や流体解析、電磁界解析などのCAE技術を適切に統合しながら、効率的な設計を進める必要があります。
技術継承と人材不足
先進国では少子高齢化に伴う労働人口の減少が進む中、設計現場では経験豊富なベテラン技術者が第一線を退くケースが増えてきています。その結果、長年にわたって培われた知見やノウハウを、いかに若手世代へ円滑に継承し、現場で活用していくかが喫緊の課題となっています。また、CAE解析などを活用した開発の効率化に関しても、短縮される設計スケジュールと複雑化する製品仕様の狭間で、解析スキルを持つ技術者の育成や、十分な計算リソースの確保といったインフラ面での新たな課題が顕在化しています。
Multi-Sigma®による問題解決
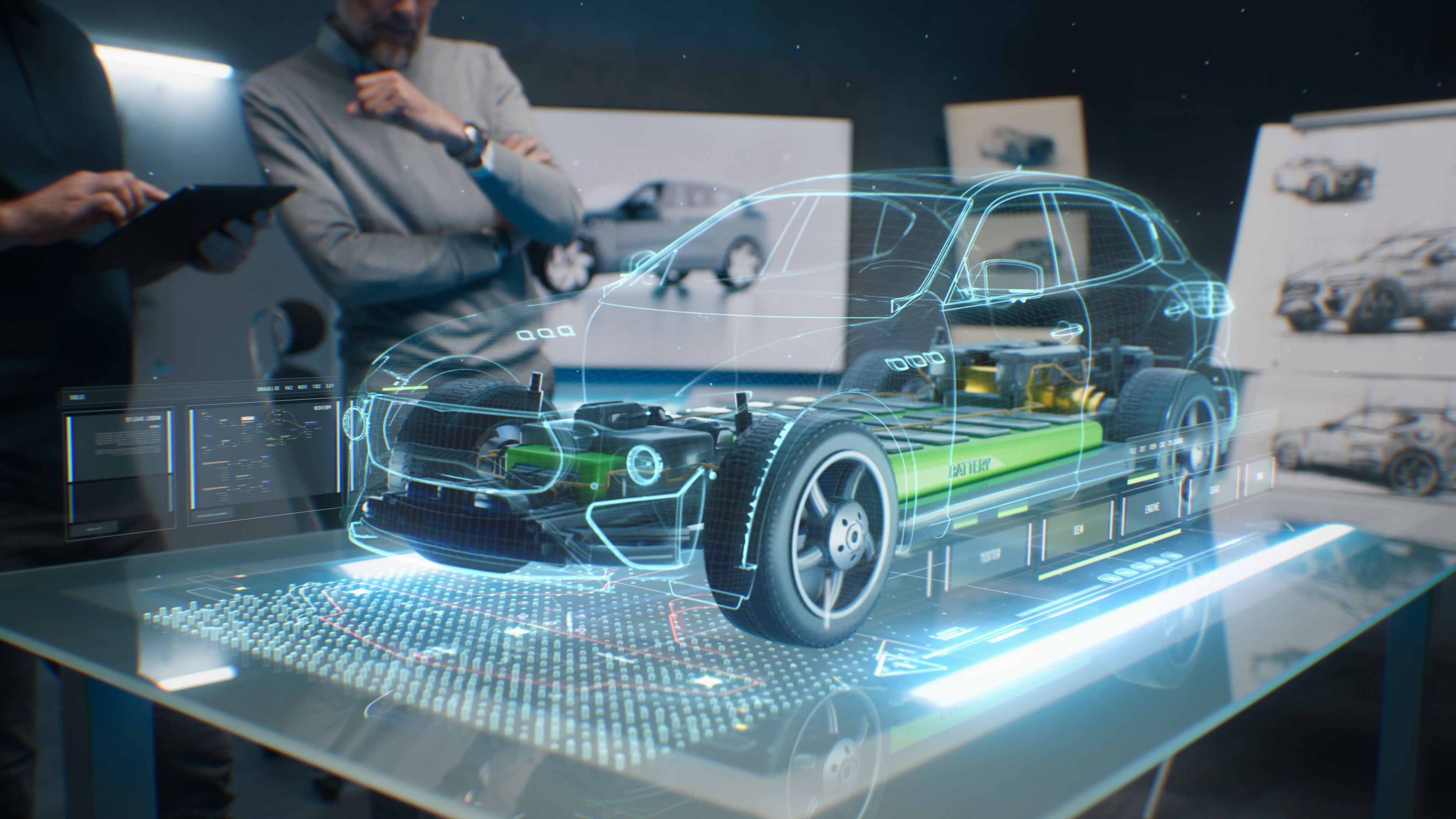
ばらつきを考慮したロバスト最適化
製品は多様な使用環境や製造条件のばらつきの中でも、安定した性能を発揮する必要があります。これは「ロバスト性」と呼ばれる設計品質の一要素であり、従来は十分な検討が難しい領域でした。Multi-Sigma®では、設計因子と性能指標の関係をAIが学習することで、高度なロバスト解析を効率的に実施可能です。複数の目的変数(例:品質・強度・コスト)に対する多目的ロバスト最適化にも対応しており、設計者はこれまで手が回らなかった領域にも踏み込んだ設計検討が行えます。
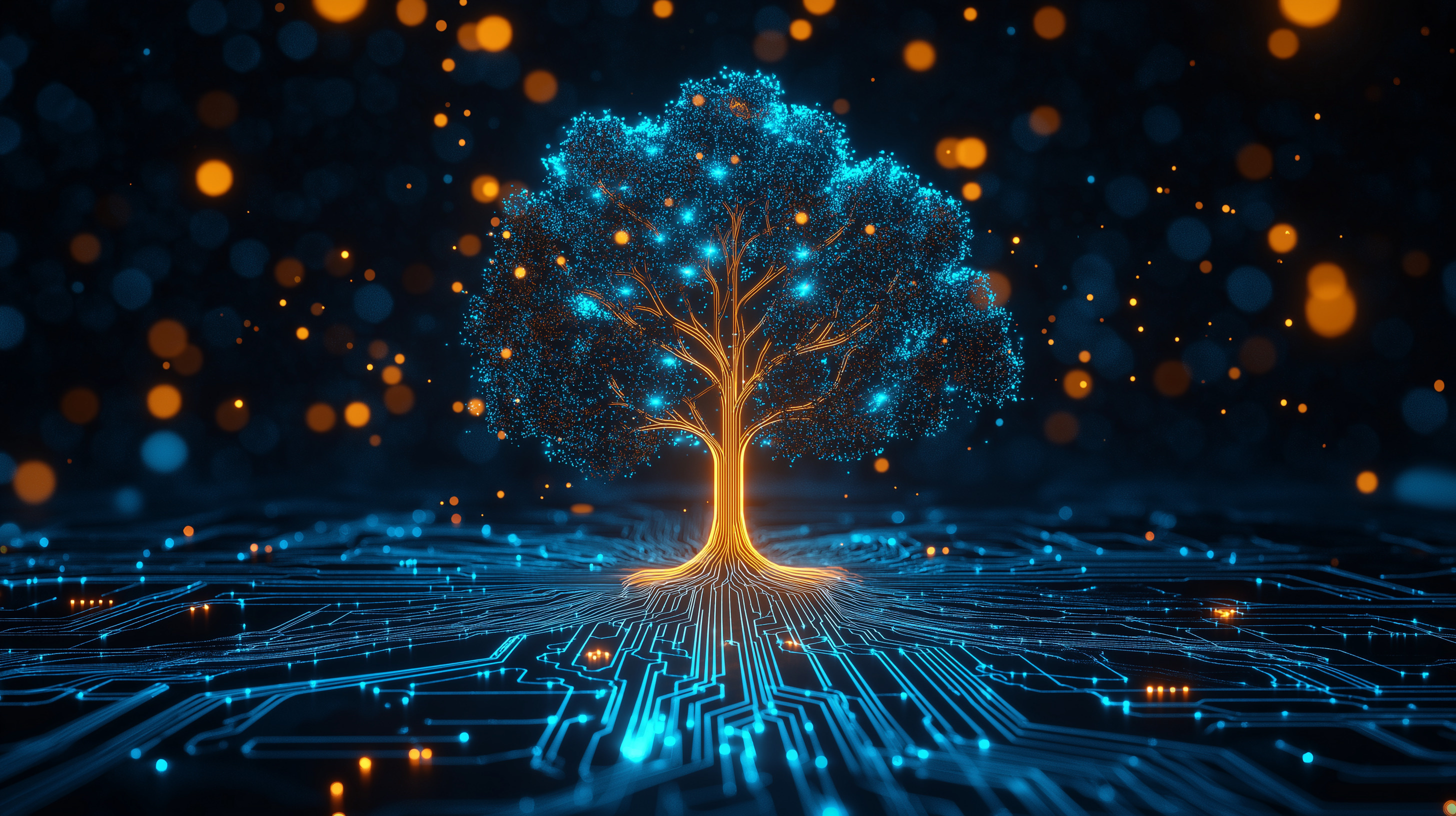
製品設計ライフサイクルの最適化
高度化・複雑化が進む製品開発の現場では、構想設計からシステム設計、部品レベルの設計・検証、さらには全体の性能評価に至るまで、設計フェーズが多層化しています。それぞれの段階には異なる専門領域のステークホルダーが関与し、シミュレーションや評価結果が次のフェーズの意思決定に密接に関わります。Multi-Sigma®は、構造解析や流体解析などのCAEデータをもとに、少量データからでも高精度なAIサロゲートモデルを作成することができます。これらのモデルを活用して、ロバスト解析や多目的最適化を実施することで、設計工数を大幅に削減可能です。また、各シミュレーションから得られた複数のサロゲートモデルを連結する「AI連鎖解析」機能により、全体最適設計にも貢献します。さらに、制御シミュレーションへの学習済みAIモデルの組み込みも可能であり、製品全体の性能検証にも活用できます。
AIモデルの安全な共有と活用
開発の効率化には、関係者間でのシミュレーションモデルの共有が重要ですが、シミュレーションモデルは企業秘密やノウハウの塊であり、共有には高いハードルが存在します。Multi-Sigma®で作成されたAIサロゲートモデルは、 Multi-Sigma®の内部では要因分析などの説明性を保持しながらも、エクスポート後は設計意図を秘匿できるため、高いセキュリティを確保したまま共有が可能です。これにより、パートナー企業や他部門との連携が促進され、製品設計の全体最適に向けた取り組みを強力に後押しします。
Multi-Sigma®を導入するメリット
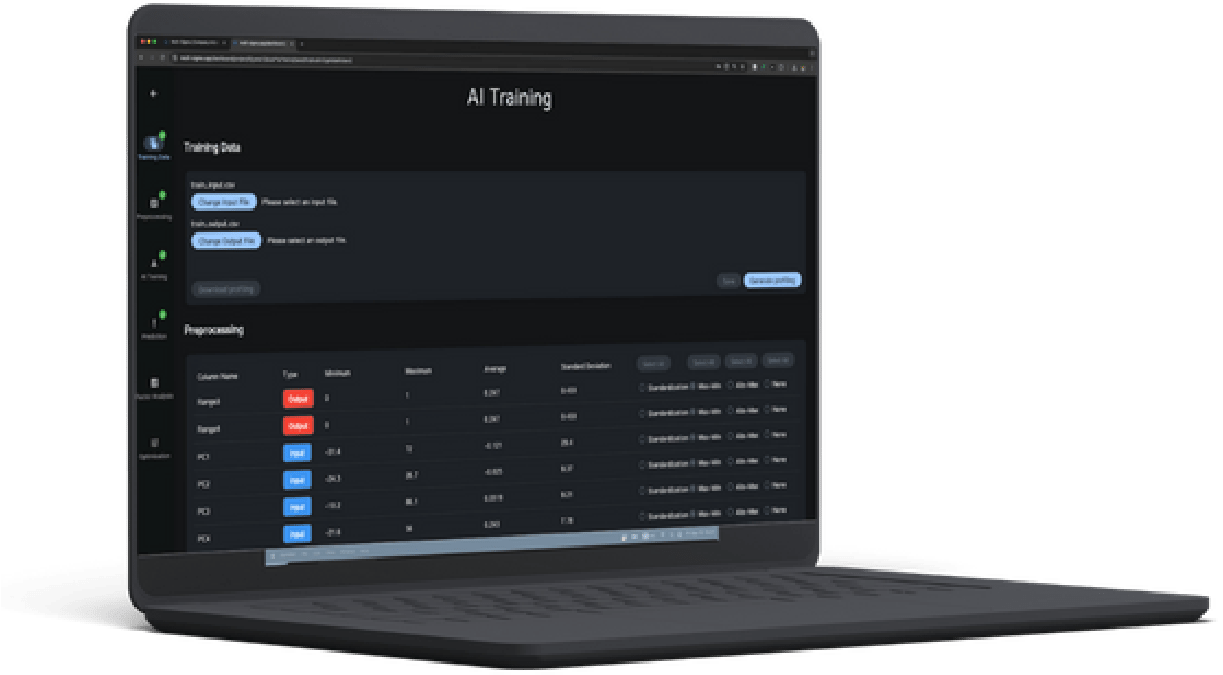
必要最小限のデータからサロゲートモデル作成
Multi-Sigma®は、限られた実験結果やシミュレーション結果をもとに、高精度なAIサロゲートモデルを効率的に構築できます。従来のAI導入に伴う準備負荷を大幅に軽減し、製品設計の効率化とプロセス全体の合理化を実現します。
多目的最適化やロバスト解析を簡単に実行
AIの柔軟性と、クラウドベースで提供されるMulti-Sigma®の高い計算性能を組み合わせることで、多目的最適化やロバスト性評価など、従来は専門知識と多くの時間を要した解析も、直感的な操作で簡便に実施可能です。
説明できるAI (XAI)
製品設計では、たとえ小さな設計変更であっても、根拠の明示が求められます。Multi-Sigma®は独自の要因分析機能により、どの設計因子が性能にどのように影響しているかを定量的に提示します。それにより設計者は設計意図を明確に保ちながら、安心してAIを活用できます。
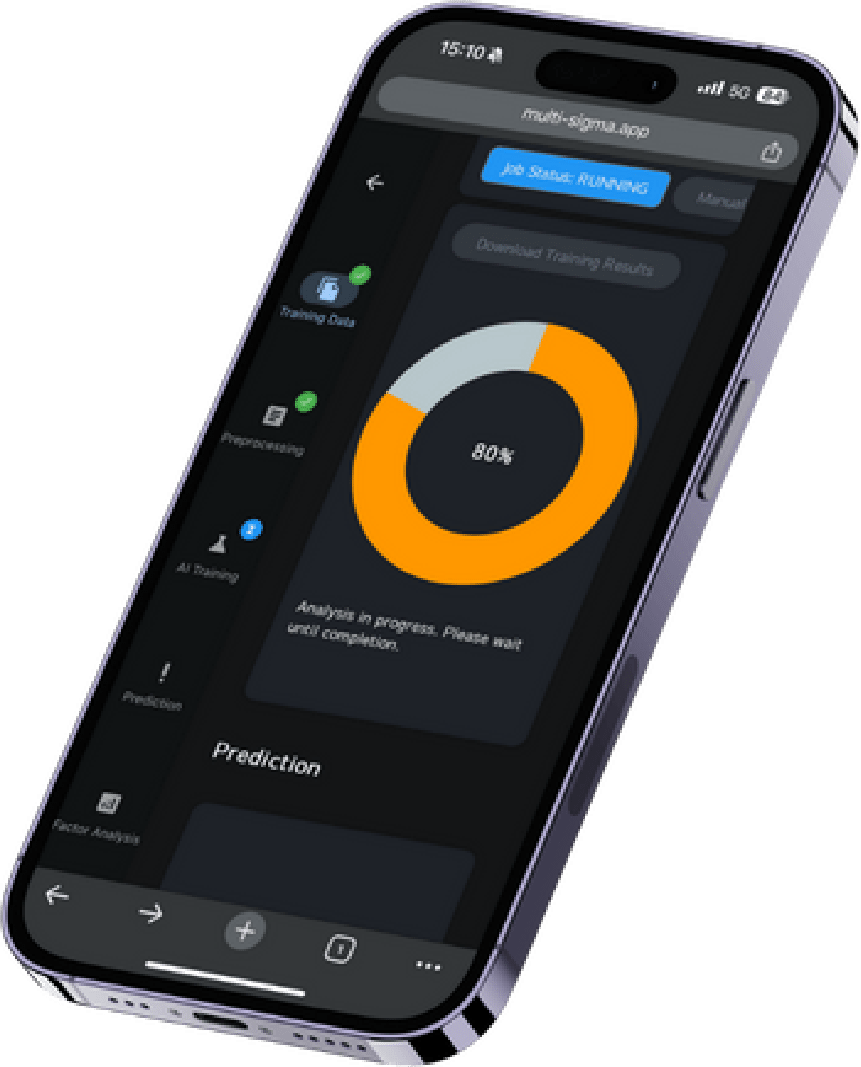
ノーコード×クラウドによる手軽な導入
Multi-Sigma®はプログラミング知識を必要とせず、GUIベースの操作で高度な解析が可能です。日々多忙な設計者でも、画面上のガイドに沿って操作するだけで、一連のAI解析が実施できます。クラウド上で動作するため、専用の計算機を用意する必要もなく、既存のPCブラウザからすぐに利用を開始できます。
AIモデルの連結による連鎖解析
Multi-Sigma®では、複数のAIサロゲートモデルを連携させて解析を行う「AI連鎖解析」が可能です。たとえば構造、流体、熱など異なる物理領域のモデルをつなげて最適化を行うことで、試行錯誤の手戻りを最小化できます。さらに、モーターとそれに接続されたファンのように、複数部品の設計因子と性能を学習させたモデルを連結することで、システム全体の性能を考慮した統合設計が可能になります。
制御シミュレーションとの連携
Multi-Sigma®で作成したAIサロゲートモデルは外部エクスポートにも対応しており、制御シミュレーションなど他の解析環境へ容易に組み込むことができます。これにより、コンポーネントレベルのCAE結果をシステムレベルに展開し、制御系を含めた製品全体の設計・評価への応用が可能となります。