Solution
Material Science
In materials science, leveraging AI for data analysis is gaining recognition as a powerful tool for assessing material properties and discovering novel materials. Significant strides are being made in the fields of Materials Informatics (MI) and Process Informatics (PI). This article highlights the challenges in the industry and discusses how the application of Multi-Sigma® can effectively address these issues.
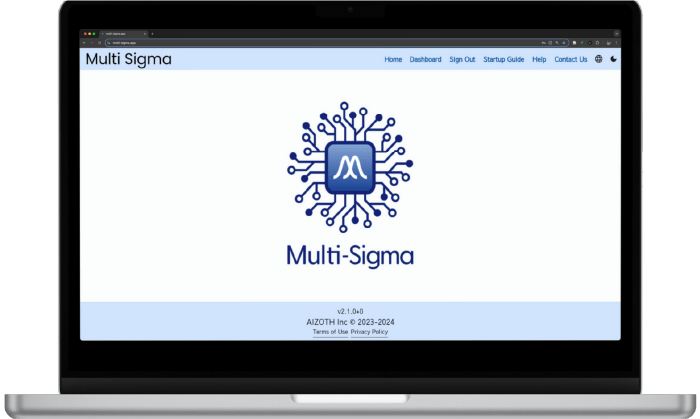
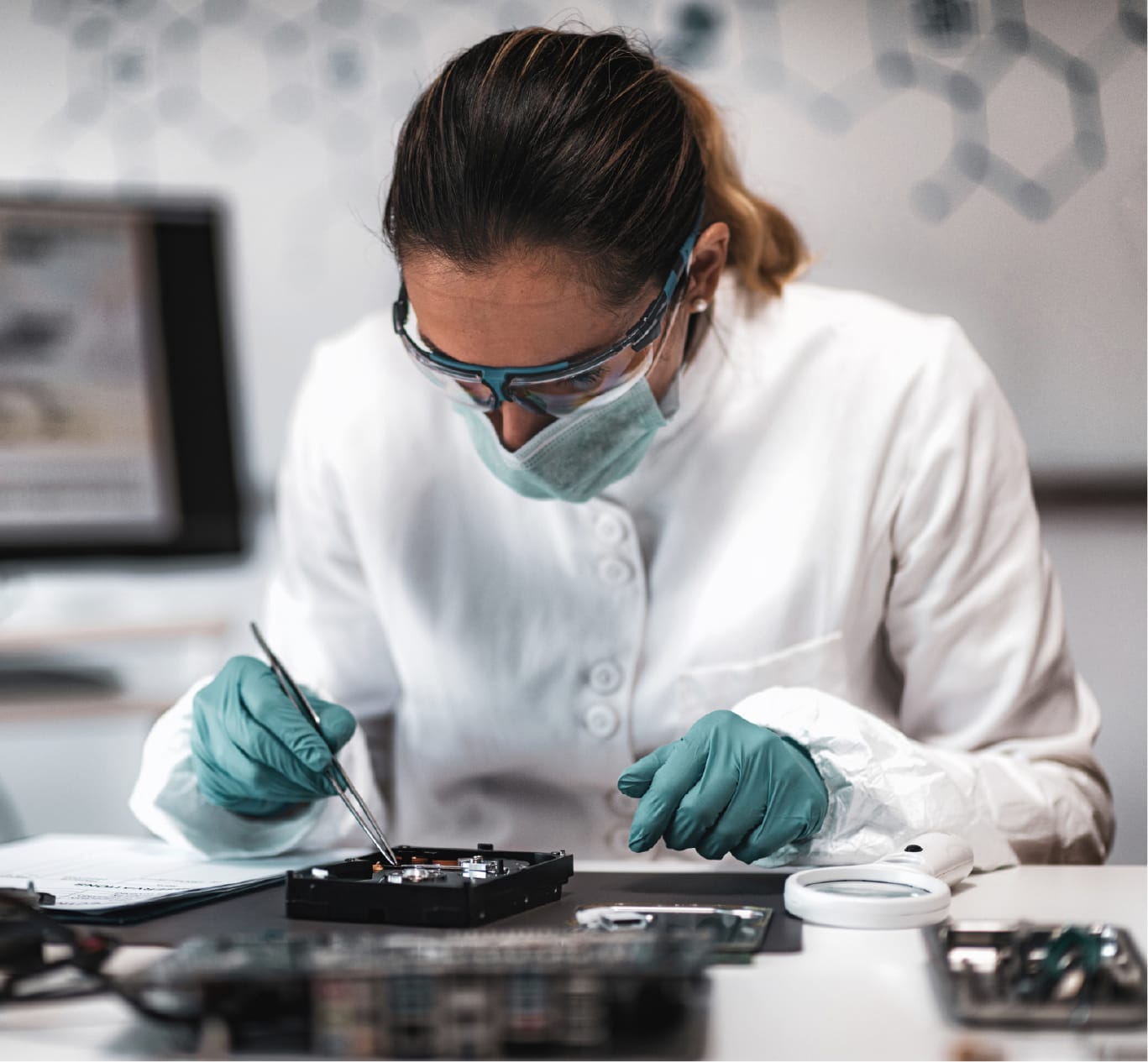
1. Challenges in the materials science industry
a. Lack of data and presence of bias
While efforts to implement lab automation using data-driven approaches and digital laboratories are actively progressing, challenges such as a lack of high-quality datasets and the predominance of data biased toward specific materials and experimental conditions remain critical challenges. In such cases, it becomes inevitable to rely on existing data for analysis instead of synthesizing new materials, thereby exacerbating the bias. These problems adversely affect AI model training and optimization, ultimately reducing prediction accuracy.
b. Treatment of diverse materials
In the design and synthesis of nanomaterials, ceramics, and metallic materials, careful consideration of the complex interactions between material composition and external synthesis conditions is essential. The properties of these materials often depend significantly on subtle changes in external factors such as temperature, pressure, and chemical environment, in addition to their microscopic composition and structure. Therefore, accurately understanding and modeling the interactions between controllable variables (e.g., synthesis temperature, reaction time, catalyst quantity) and resulting material properties (e.g., strength, thermal conductivity, electrical characteristics) remains an unresolved challenge. Addressing this challenge is critically important in materials science, as it directly impacts the efficient design of novel materials and the development of high-performance materials.
c. Limitations of computational resources
Molecular dynamics simulations and first-principles calculations are widely utilized as powerful methods for predicting the properties of novel materials and assisting in their design. However, these methods often require substantial computational resources, with high computational costs and long processing times posing barriers to practical implementation. Additionally, while these simulation techniques are generally well-suited for making predictions based on physical models, they are less effective for inverse analytical approaches aimed at optimizing target variables (e.g., strength, conductivity, thermal conductivity). Consequently, it remains challenging to automatically explore the optimal compositions, structures, and external conditions necessary to achieve desired material properties, often necessitating manual trial-and-error. To overcome these limitations, integrating AI and data-driven approaches has become essential.
d. Interpretation of results
Explaining the rationale behind prediction outcomes is vital for ensuring scientific reliability. In the field of materials science, the interpretation of prediction outcomes plays a particularly critical role. This is because accurately understanding the results and uncovering the underlying causal relationships and mechanisms can provide new insights for material design and process optimization. Conversely, when predictions function as a “black box” and the reasoning behind them cannot be clearly explained, it not only undermines the reliability of applying the results but also poses significant challenges to improving the predictive model and expanding its applications. For these reasons, the introduction of methods to enhance explainability is considered crucial. Explainable predictive models not only greatly enhance their practicality as complements to experimental results and as guides for new material discovery but also serve as key enablers of acceptance in both academic and industrial applications.
2. What Multi-Sigma® can do for the materials science industry
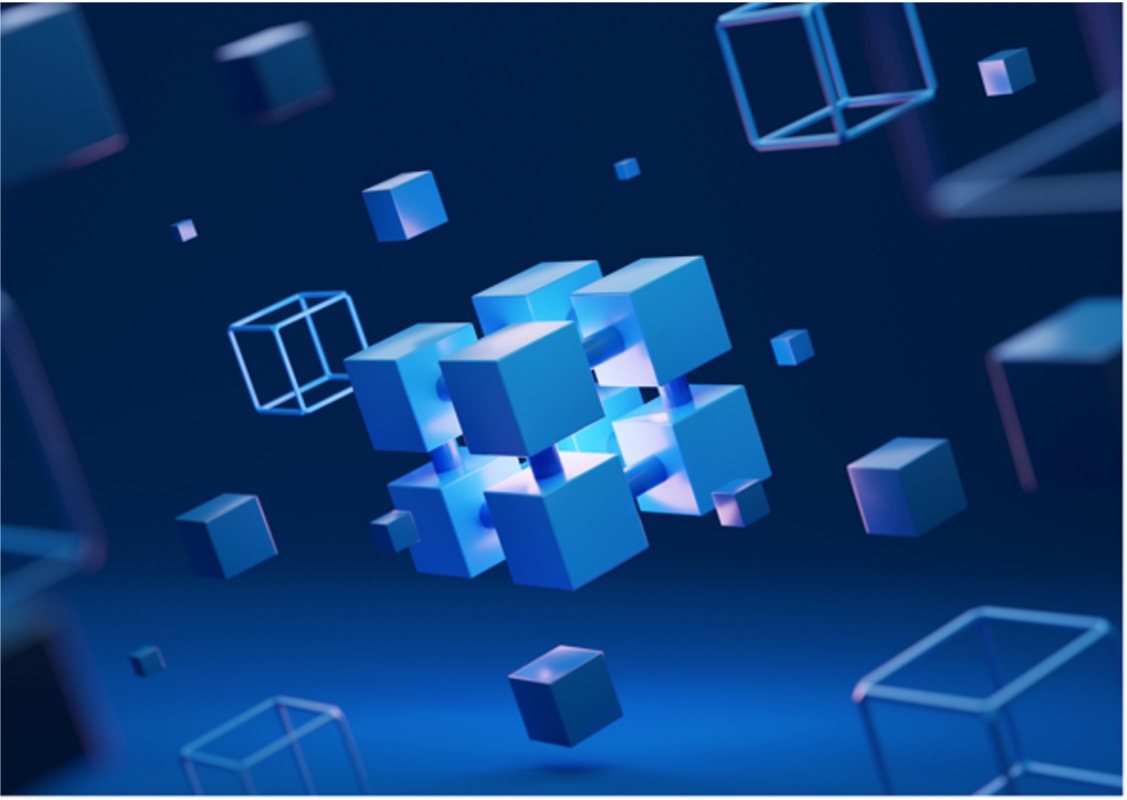
a. Start with minimal data
Multi-Sigma® enables the construction of AI models using small datasets. With its auto-tuning functionality, which automatically adjusts the hyperparameters of neural networks, it is possible to build highly accurate models even with limited data. Additionally, for imbalanced datasets where specific data instances are underrepresented, the imbalance adjustment feature can mitigate data bias, allowing for high-accuracy predictions and optimizations even for data with fewer instances. Furthermore, when training data for AI model construction contains missing values, the system’s automated imputation capabilities can fill in the gaps using various methods, enabling model development that includes such data.
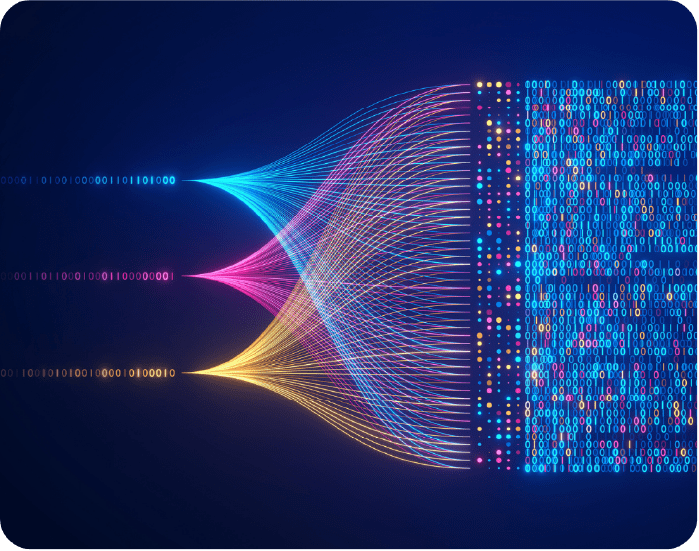
b. High-accuracy predictions and optimization
Multi-Sigma® is a powerful AI analysis tool that can be applied to numerical analysis for various materials. Numerical data on input and output parameters for material design and synthesis enables the modeling of interactions between these inputs and outputs using deep learning techniques—without the need for programming. Furthermore, AI models built with Multi-Sigma® achieve highly accurate predictions. By leveraging Multi-Sigma®’s optimization functionality, it is also possible to provide practical solutions for designing new compounds with desirable properties. These solutions allow for efficient R&D by screening among numerous combinations of input parameters and conducting additional experiments or numerical computations based on the results.
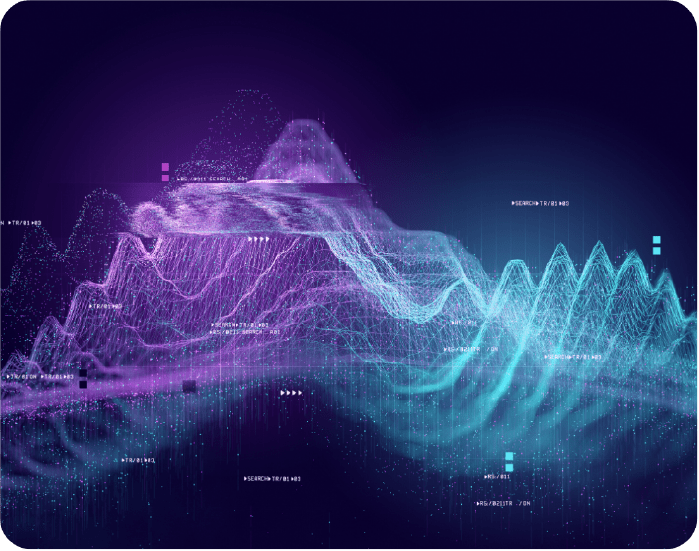
c. Construction of surrogate models
Multi-Sigma®’s AI models can replace highly complex simulation models that demand significant computational resources. In materials science, simulations based on molecular dynamics or first-principles calculations often require substantial time and computational power. With just a small set of simulation results, Multi-Sigma® is capable of building surrogate models (also known as emulators). This approach facilitates both precise predictions with AI models and comprehensive optimization, enabling efficient data analysis while making the most of available simulation resources.
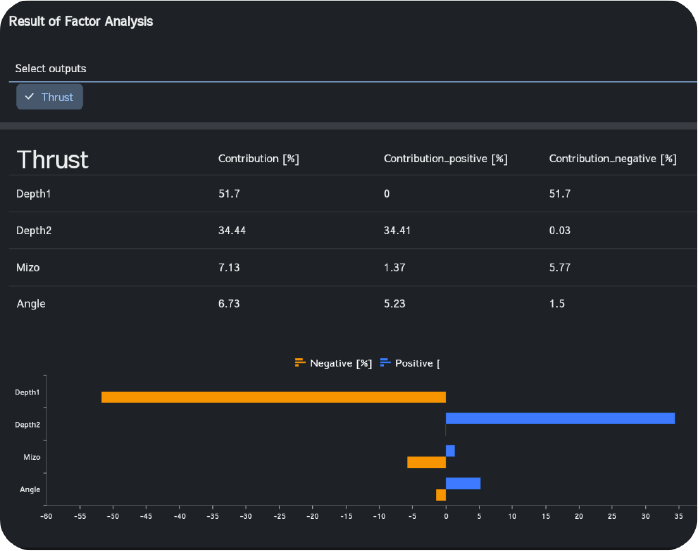
d. Factor analysis function enables white-boxing
Multi-Sigma® is equipped with a factor analysis function that quantifies and analyzes both the positive and negative effects of inputs on outputs. This functionality clarifies how each input parameter influences individual output parameters. For example, in chemical synthesis, it can interpret how various input parameters—such as synthesis time, synthesis temperature, solvent, and synthesis ratios—impact the outputs. This capability aids in uncovering the mechanisms underlying the relationships between inputs and outputs.
Advantages of Multi-Sigma®
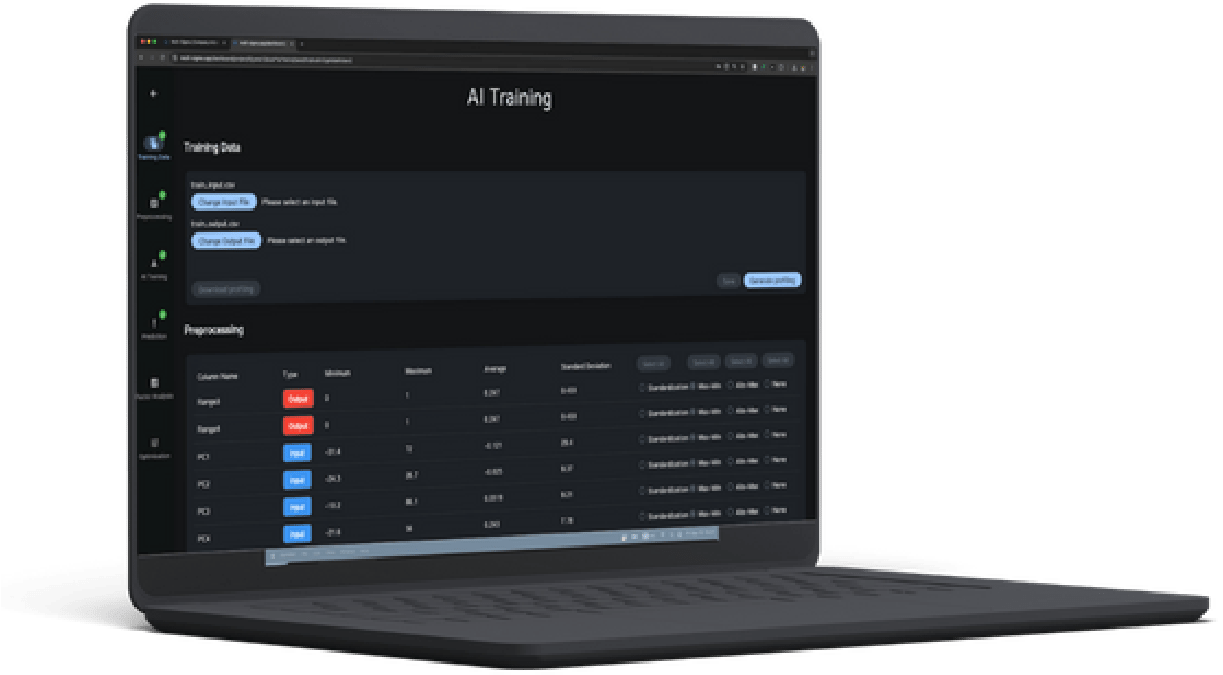
a. Deep learning with minimal data
Multi-Sigma® enables modeling and analysis from small experimental datasets, reducing experimental effort and shortening R&D cycles across various fields.
b. High-precision prediction
Offering high-accuracy predictive, factorial, and optimization capabilities, Multi-Sigma® allows for realistic and effective analysis based on experimental data.
c. Multi-objective optimization
Capable of exploring up to 200 inputs to satisfy 100 outputs, Multi-Sigma® finds optimal solutions for multiple competing goals simultaneously, aiding in new material development and improving manufacturing efficiency.
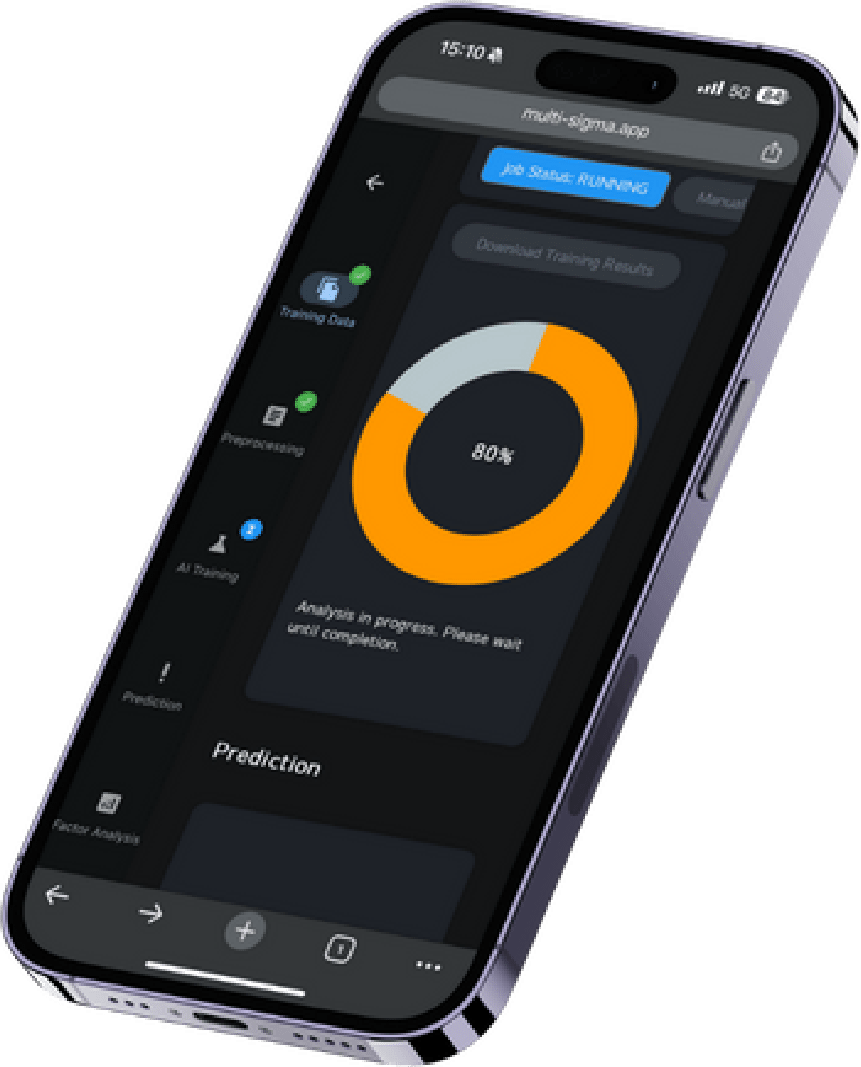
d. Explainable AI (xAI)
Multi-Sigma® includes a factorial analysis function that reveals which inputs affect which outputs, their extent, and whether the impact is positive or negative, enabling users to interpret results and understand internal mechanisms.
e. No-code and cloud-based
Requiring no programming skills, Multi-Sigma® provides an intuitive interface for data analysis with just a few clicks. As a cloud-based tool, it continuously updates with new features and bug fixes based on user feedback.
f. Chain analysis
By linking inputs and outputs across multiple processes, Multi-Sigma®’s chain analysis function chains multiple AI models for comprehensive analysis, enhancing AI performance and revealing process mechanisms.