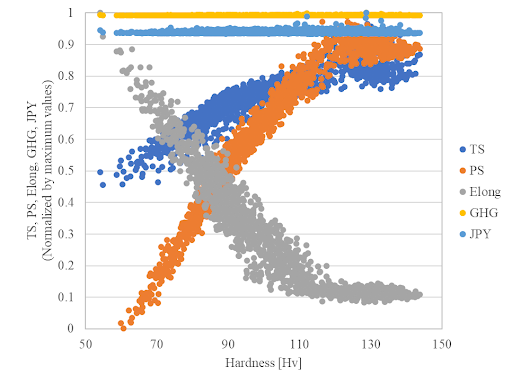
Aizoth Co., Ltd. (Headquarters: Tsukuba, Ibaraki), was chosen for the “Aluminum Material Advanced Resource Circulation System Construction Project” implemented by the New Energy and Industrial Technology Development Organization (NEDO) under the theme of “Development of Upgrade Recycling Technology for Aluminum Resources Toward the Construction of a Resource Circulating Society.” The project aims to develop upgrade recycling technology to regenerate aluminum resources and produce recycled aluminum with high functionality.
Aluminum is known for its lightweight, corrosion resistance, easy processing, and high thermal conductivity, making it a sought-after material for lightweight applications such as automobiles. However, in the current recycling processes, impurity concentrations increase with each recycling cycle, leading to a decrease in the material’s strength, ductility, and other functions, ultimately resulting in landfill disposal. Additionally, while some aluminum is recycled, the primary metal for high-purity extrusion materials is consistently reliant on imports from overseas.
Challenges
・From experimental data, it is necessary to estimate the cost and environmental impact for each experimental condition and optimize the manufacturing conditions in a multi-objective manner along with the objective variables related to functionality.
・Only 18 pieces of experimental data are available.
・Optimizing the conditions of a complex process is required, where there are 6 parameters for manufacturing conditions and 6 parameters targeted for objectives.
Solutions
A practical Life Cycle Assessment (LCA) evaluation was conducted, considering factors like scale effects, to estimate costs and environmental impacts for each experimental condition. The AI was trained on 18 data points encompassing six experimental conditions within the aluminum upgrade recycling process, specifically in the heat treatment stage, including impurity concentration, temperature, time, and pressure. Experimental results included material properties such as hardness, tensile strength, and yield strength, along with six objective variables related to greenhouse gas emissions and cost. Utilizing the Multi-Sigma auto-tuning technology, the AI model was trained to create a high-precision neural network prediction model while suppressing overfitting. The resulting prediction model, coupled with a multi-objective genetic algorithm, was then employed to explore optimal processing conditions that maximize metal functionality while minimizing greenhouse gas emissions and cost.
Results
From just 18 sets of experimental data, we successfully explored manufacturing conditions that not only result in greenhouse gas emissions of 1/10 or less compared to primary metal production but also keep costs in check. Furthermore, these conditions achieve functionality comparable to high-tensile steel sheets.
The Multi-Sigma Advantage
Ready to revolutionize your Chemical Engineering processes? Contact us to start your free trial with AIZOTH’s Multi-Stigma today. Experience the difference as you elevate decision-making, unlock unprecedented benefits, and redefine the future of Chemical Engineering with the power of AI.
Start Your Free Trial Now