生産プロセスのモジュール化・システム化に対応するためのAI連鎖解析による仮想実験
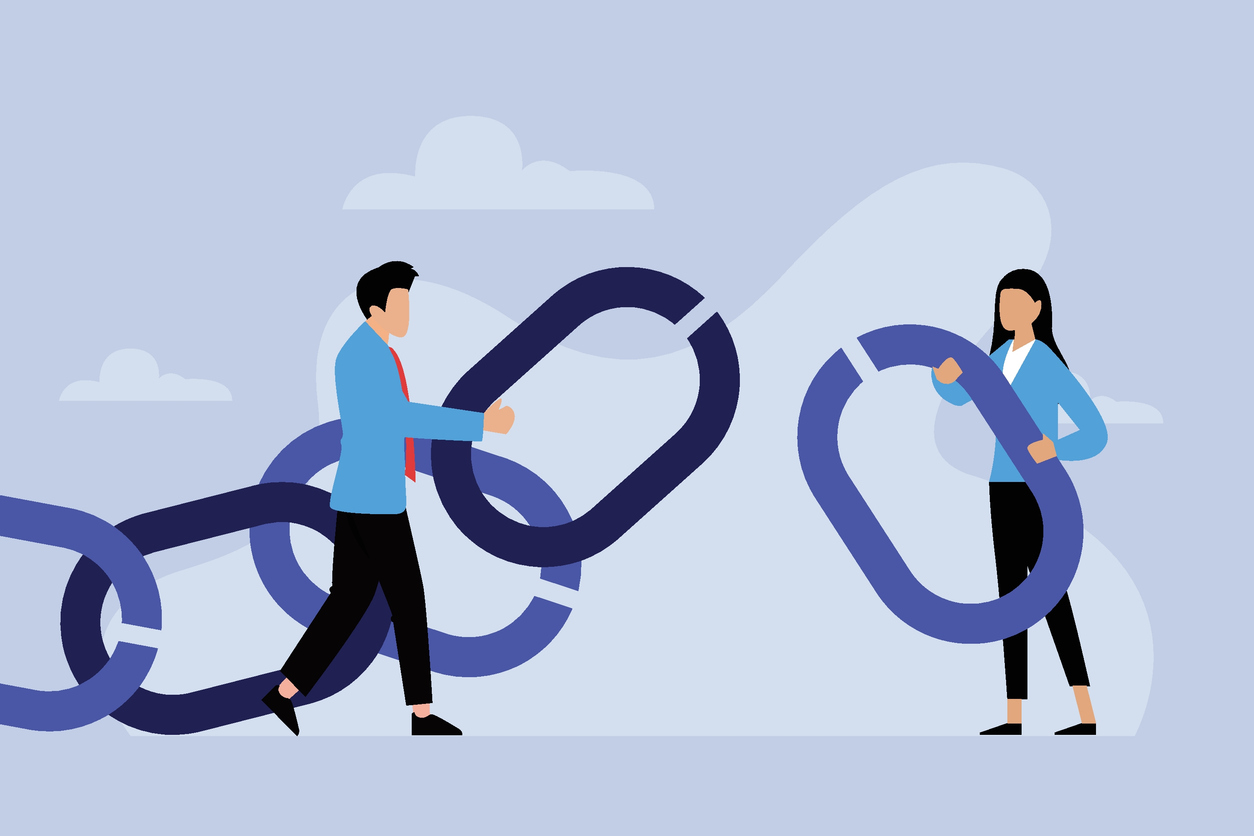
株式会社エイゾスは、世界初となる、革新的なAIの連鎖解析システムを開発いたしました。本解析システムは、同社が国際特許を出願中の技術で、ノーコードAI解析プラットフォーム「Multi-Sigma」において2024年7月31日よりご利用いただけます。
本稿では、なぜAIの連鎖解析が必要か、それを現実の研究開発の現場でどのように活用できるのかについて、紹介したいと思います。
複数工程の生産プロセスに対するAIの解析
まず開発の背景ですが、当たり前の話ではありますが、ものづくりの現場では、一つのプロセスだけで最終製品ができることは稀で、一般的には複数の工程を経て、最終製品が出来ます。そのような複数工程による生産システムに対して、これまでは、複数の工程を一つのブラックボックスとして扱い、システム全体のインプット、アウトプットを一つの実験データにまとめて、一つの機械学習のモデルで学習していました(図1)。

図1.複数工程のブラックボックス化
既存の方法の課題
この方法は、モデルが簡易で、少ない工数で解析できる一方で、いくつかの課題があります。第一に、複数工程のうちの一つでも、実験条件やプロセスの変更があった場合に、システム全体の実験データを取り直す必要があることです。システムが複雑かつ大規模になればなるほど、プロセスの改修に伴う実験データの取り直しのリスクが大きくなります。第二に、複数工程を一つのブラックボックスとして表現するために、プロセス内部の現象の理解が難しくなります。仮に最終製品に不良が発生した場合に、それがどのプロセスに起因するものかわからなければ、改善の方策を検討することが出来ません。最後に、全ての工程を一つの実験データにまとめた場合、全てのシステムを稼働させないと実験データが得られないので、システムが大規模になると、実験の実施が難しくなります。
AIの分割と組合せ
前述のような課題を解決するために、まず最初に複数の工程を個々のプロセスに分割し、それぞれに対して実験を実施し、AIを作成し、それらをつなぎ合わせて一つのシステムとして解析できるAIの連鎖解析システムを構築しました(図2)。このつなぎ合わせたシステムを使って、予測・要因分析・多目的最適化を実行できます。
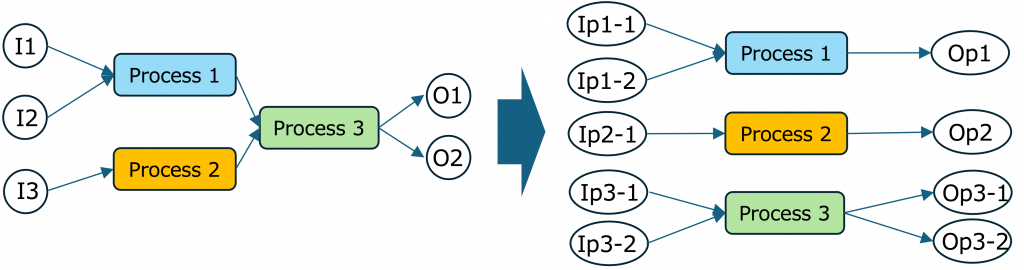
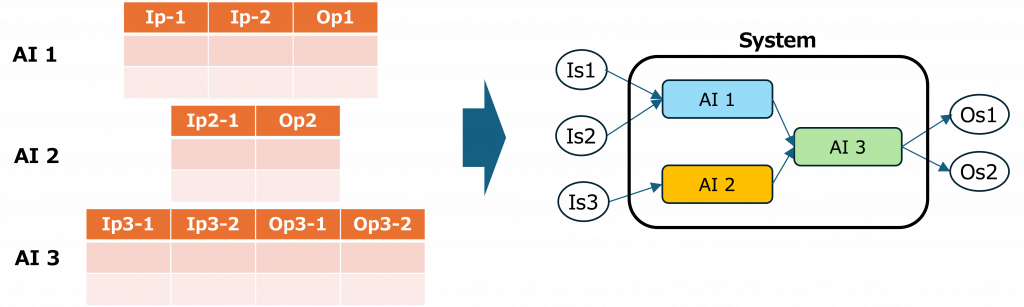
図2.複数工程の連鎖解析
連鎖解析のメリット
このようにプロセスごとにモデルを作成することで、例えば仮にProcess1がアップデートされたとしても、その出力値のパラメータが過去のデータと共通であれば、Process1のみモデルをアップデートし、過去のProcess2,Process3のモデルと接続できるので、システム全体の実験をやり直す必要がありません。また、プロセスごとに実験を行えばよいので、システム全体を動かして実験データを取得する必要がありません(もちろん、システム全体を動かして一度で全てのプロセスのデータを取得することも可能です)。さらには、プロセスごとに要因分析を行うことができるため、システム内部のメカニズムを理解しやすくなります。最後に、なによりも重要なのは、このようにプロセスごとにAIを分割しておくことで、個々のAIを、他の事例にも流用しやすくなります。
過去のAIを利活用し、複雑な工程を表現
個々のAIが表現するプロセスを小さく、シンプルにすることで、AIを共通化することが可能となり、それらを組み合せることで、より複雑なシステムを表現できるようになります。逆に、複雑に組み合わされたプロセスを一つのモデルにしてしまうと、AIを共通化し、他のプロセスと組み合せることが難しくなります。レゴブロックのように、個々のブロックをシンプル、かつ小さくすることで、それらを組合せて様々な形を表現することが出来るのです。
今後あらゆる分野で必要とされる連鎖解析
このような、プロセスを細分化した上で、それらを組合せてシステム化するという議論は、現在、生産プロセスのモジュール化・システムという形で、あらゆる分野で進んでいます。自動車などの機械製品であれば、モジュール化は馴染みのある言葉ですし、半導体分野ではユニットプロセスやプロセスインテグレーションという言葉が使われています。化学分野であれば、プロセスシステム工学という、一つの領域として体系化されています。
以上のような動向に対応するために、AIの連鎖解析は必要不可欠なツールですが、AIをつなぎ合わせて、予測・要因分析・多目的最適化まで実行できるツールは、現在世界にMulti-Sigmaしか存在しません。ぜひ一度、お試しいただければ幸いです。